Oil and Gas
Pressure measurement in oil processing
Flange type chemical seal with high soft membrane with pressure and differential pressure transmitter, using the original cap flanges (AppBe_Oe_034)
for refineries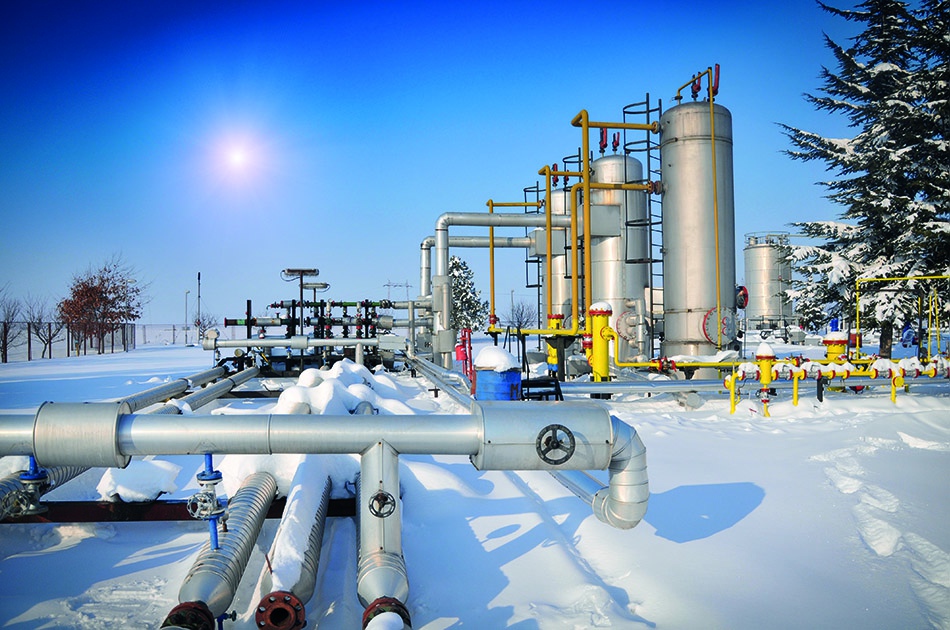
The problem:
In former plants, it had been necessary to install an additional trace heating for the capillary line and the chemical seal to ob-tain a functioning and accurate measurement. Furthermore, the original cap flanges had to be replaced by volume-reduced cap flanges that were produced in one-off production.Our solution:
Compared to the sinus membrane, our high-soft membrane with its performance can compensate the additional large oil volume in the cap flange (9 cm3 per side) temperature-wise, with the result that no additional error occurs that is caused by the ambient temperatures −28 / +70 °C (−18.4 / +158 °F). This error would have to be viewed more critically at an ambient temperature of +70 °C (+158 °F) than +400 °C (+752 °F) (medium temperature) at the chemical seal, due to the large oil volume in the cap flange. In combination with our special oil [−40 / +400 °C (−40 / +752 °F)], an operation is made possible without the trace heating, which is usually required. The trace heating can also be omitted at a process connection of PN 50, which would also lead to further cost reductions.Our advantages at a glance:
- No need of trace heating
- No need of volume-reduced cap flanges that are produced in one-off production
- No additional errors
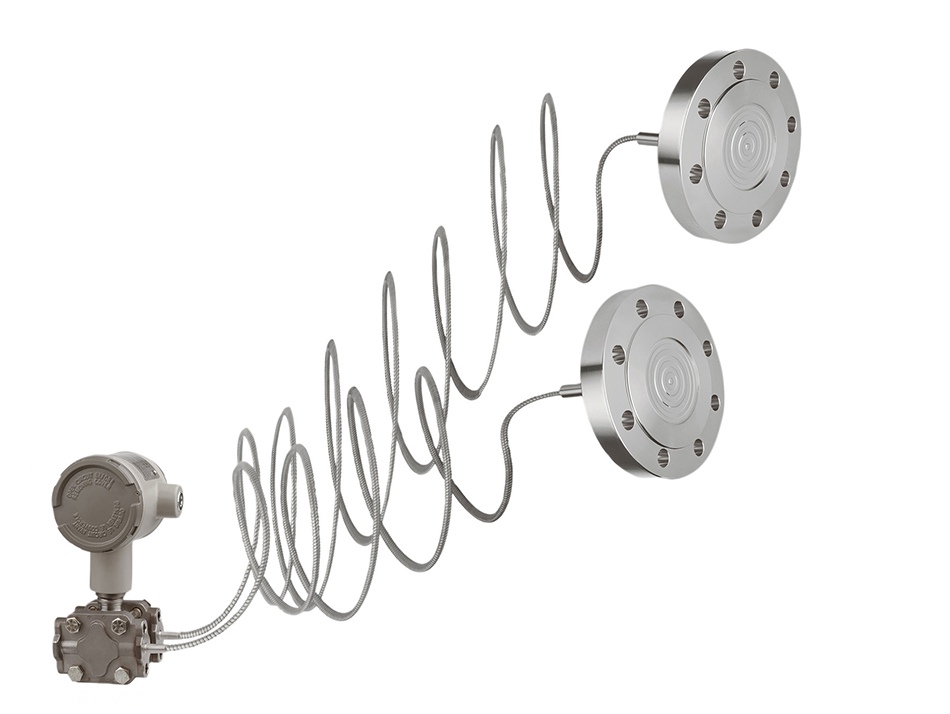
Our instrument in detail:
No trace heating necessary: MDM 7510 DN 80- Up to 10-times improved temperature behaviour [up to tA max. +400 °C (+752 °F)]
- Temperature-related additional error (mbar/10 K) in the range of −40 °C up to +400 °C (−40 °F up to +752 °F)
- We can guarantee these values if the pressure measuring instruments and the diaphragm seal are completed and filled in our factory.
Download:
Pressure measurement in gas industry
Pressure gauges for monitoring of residual pressure in gas bottles (AppBe_Oe_035)
for manufacturers of monitoring systems for gas bottles,for manufacturers of fire-extinguishing systems with gases (e.g. Inergen)
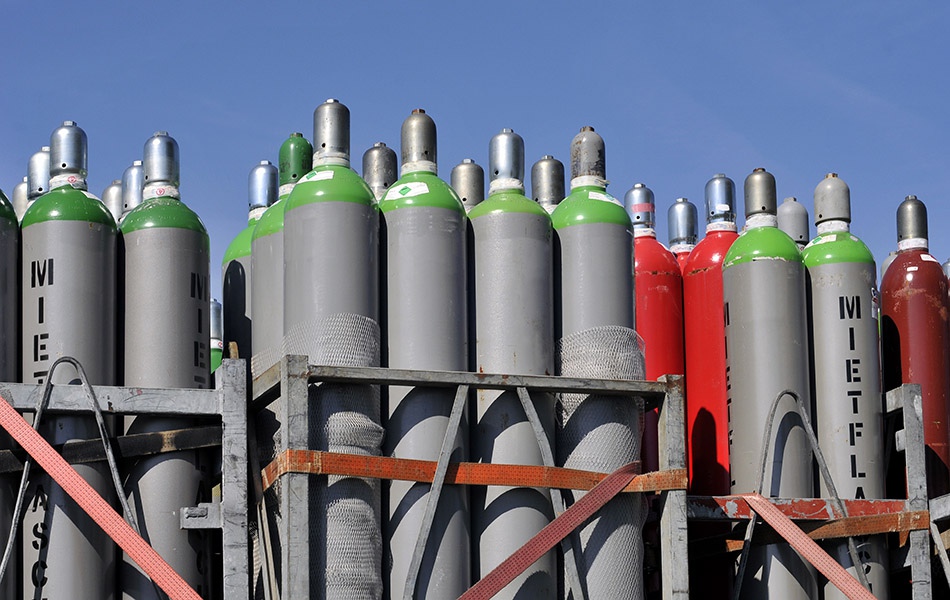
The problem:
There are two types of gas bottles:- Gas bottles with liquefied content (e.g. propane, carbon dioxide)
- Gas bottles with highly compressed gaseous content (e.g. nitrogen, oxygen, argon)
Liquefied gases change their state of aggregation upon temperature changes. The vapour pressure of the liquefied gas determines the pressure within the bottle. The filling level is determined by weighing. The residual pressure content of such a gas bottle cannot be indicated by the pressure gauge.
For compressed pressurised gases with pressure regulator* the following applies: half pressure – half full. Depending on the type of bottle, the pressure is 200 or 300 bar.
As the gases can partially be aggressive, the material has to fulfil certain requirements, dependent on the type of gas.
* The pressure regulator has two pressure indications. The first indicates the pressure of the gas bottle when it is opened (inlet pressure). With the second valve and the corresponding second indication, the pressure of the gas is controlled, which escapes from the pressure regulator (outlet pressure).
We offer the following solutions:
When using oxygen, it has to be ensured that all parts are free of grease and oil and have been adjusted residue-free with dry air, since grease and oxygen are inflammable under pressure.For non-aggressive gases, we use inner parts made of non-ferrous metal, alternatively stainless steel or Monel (upon request with helium leak test).
A gas bottle should not be emptied completely to avoid vacuum when cooling.
In order to control the remaining pressure in the bottle, we apply limit switch contact assemblies. This provides the following advantages:
- Securing the supply
- Avoidance of cleaning costs upon full drain
- Control of the min. and max. pressure at the outlet of the regulator
Our advantages at a glance:
- Materials are selected in accordance to the gas
- Limit switch contact assemblies for the control of residual pressure
- Special connection for versions with ultrapure gas
- Safety case
Our instruments in detail:
With limit switch contact assembly:- Connection thread G ¼ B (¼" BSP), ¼" NPT, M 10x1
- Special connection for versions with ultrapure gas (VCR male thread or union nut)
Examples:
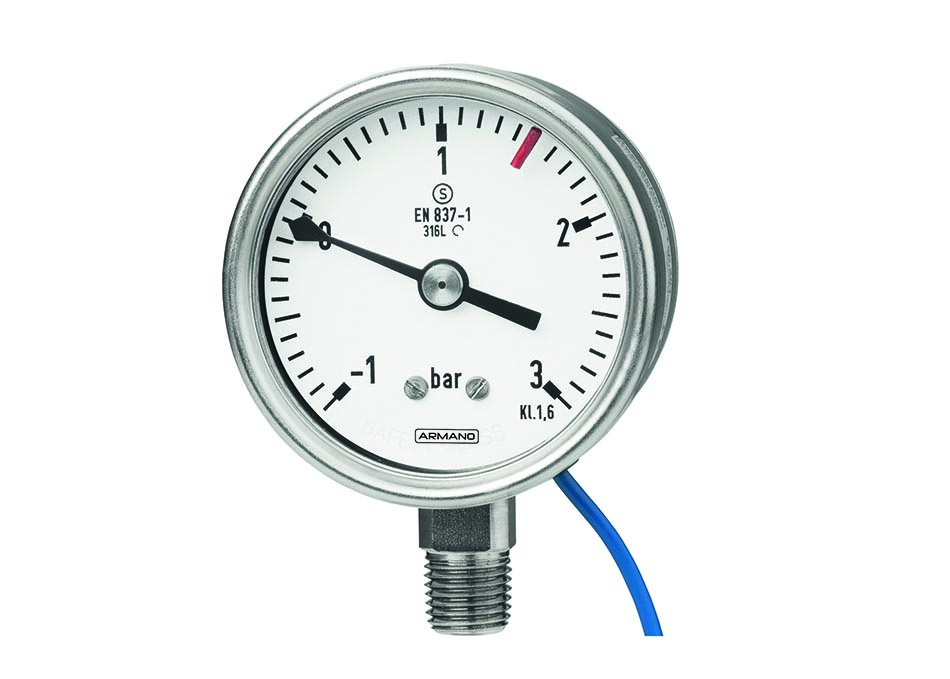
- With reed contact
- Pressure, with which the gas escapes from the bottle
- Pressure range: -1 / + 3 bar (30" Hg vac. - 60 psi)
- Outlet pressure
- Safety case S3
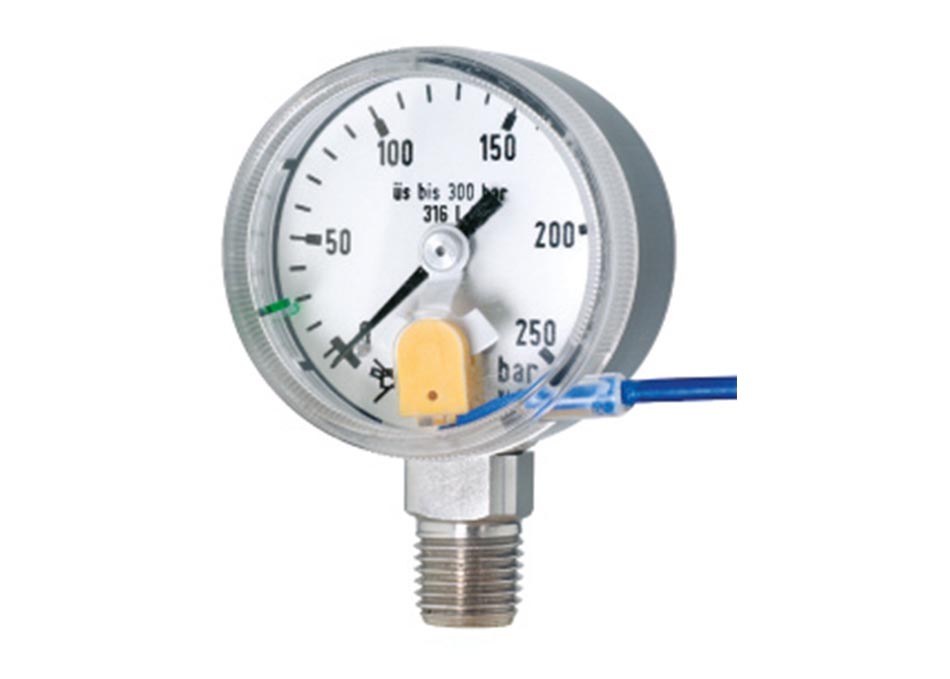
- With inductive contact
- Content pressure of the gas bottle
- Pressure range: 0 – 250 bar (0 – 3,000 psi)
- Inlet pressure
- Safety case S2
Downloads:
- Application report Pressure gauges for monitoring of residual pressure in gas bottles
- Data sheet 1610.94 Bourdon Tube Pressure Gauge RSCh 63 with indirect limit switch contact assembly (model R)
- Data sheet 1610.92 Bourdon Tube Pressure Gauge RSCh 63 with indirect limit switch contact assembly (model E and I)
Pressure measurement in alkylation units for the gasoline production
Bourdon tube pressure gauge RSChG 100 – 6 with diaphragm seal MDM 7910 in primary and secondary Monel design for the application in alkylation units (AppBe_Oe_036)
for refineries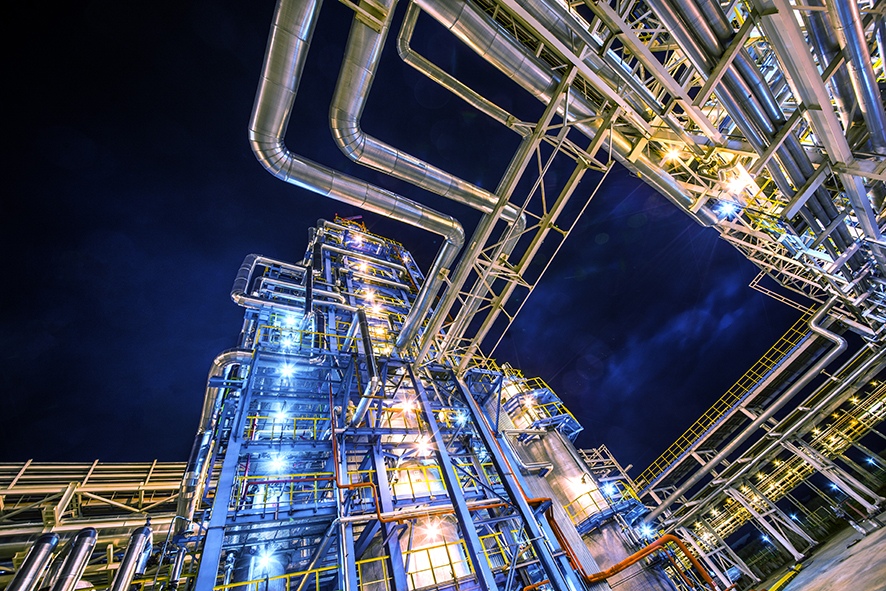
The HF alkylation unit is a key element of refining. It plays a crucial role in providing one of the most important feeds to gasoline blending.
The problem:
The significance of the HF alkylation has grown side by side with the increasing number of FCC units in refineries.Handling hydrofluoric acid, however, poses specific hazards. HF values in the air can reach high concentrations without being noticed as odour. Since HF interferes with the nerve function, it is possible that burns are not noticed immediately.
HF vapour leakage and medium leakage has to be avoided in any circumstances.
Our solution:
Monel 400, a nickel-copper alloy with high strength and outstanding corrosion resistance, is an important structural material when dealing with hydrofluoric acid. The alloy is used for instruments, valves, pumps, shafts, fittings, fasteners and heat exchangers.The Monel 400 Bourdon tube pressure gauge with chemical seal by ARMANO has been especially developed for the application in HF alkylation. Specific constructional and production-related features have been taken into account.
A redundant design and monitored manufacturing processes guarantee a reliable pressure measuring instrument for this demanding medium.
Our advantages at a glance:
- Fully welded construction – All components are welded and helium leak tested. Thus, no leakages can occur due to vibrations or temperature variation.
- Double medium barrier – Chemical seal and pressure measuring instrument are made of Monel and suitable for hydrofluoric acid. In case of failure of the first medium barrier, the pressure gauge still offers full protection against leakage of hydrofluoric acid.
- Overrange protected construction of the pressure gauge – Even after considerable overload, the measuring properties and the accuracy class 1.0 remain unchanged.
- Guaranteed water-free manufacturing process – All production steps are absolutely dry and water-free.
- Certified manufacturing process – Any mix-up of materials is precluded.
- Certified welding procedure – carried out by externally certified employees.
- Weld seam inspection – by externally qualified personnel.
- Individual certificates and documentation – for each instrument.
RSChG 100 – 6vDW
(model overview 1000 and data sheet 1600)
- Case: with bayonet ring stainless steel
- Nominal case size: 100 mm (4")
- Process connection:
• bottom connection
• welded connection piece d8x5
• material 2.4360 / N04400 (Monel 400) - Wetted parts: 2.4360 / N04400 (Monel 400)
- Pressure ranges: e.g. 0 – 40 bar (S),
DIN EN 837-1 (dial inscription) - Version: overrange protected
- Accuracy: class 1.0
- Movement: stainless steel
- Window: laminated safety glass
- Case filling: glycerin 86.5 %
- Marking according to ATEX with II 2GDc
- CE marking (with or without)
- Adjustment with dry air (water-free)
(model overview 7000 and data sheet 7935)
- Process connection:
• G 1⁄2 B with orifice Ø 10 mm (0.39”)
• material 2.4360 / N04400 (Monel 400) - Wrench flat: AF 21
- Nominal pressure: PN 250
- Material body: 2.4360 / N04400 (Monel 400)
- Material membrane: 2.4360 / N04400 (Monel 400)
- Filling fluid: FO1 (halocarbon)
- Operating temperature: tA +20 °C
- Ambient temperature: tU −20 to +60 °C
- Inspection certificate 3.1 according to EN 10 204 on the material tests for bar stock
re-stamping certificate - Material quality certificate for the membrane including heat treatment condition
- Chemical seal with batch number
body and membrane stamped at the coverage - Water-free including sticker “dried and water-free”